金属ガスケットの製品を紹介したします。
メタルOリングについて
メタルOリングとは、別名メタル中空Oリングと言われることもあります。形状はまさに外観見ればOリングですが、従来のゴムOリングとは異なり、金属製のOリングです。
当然ですが、ゴムのような柔軟性はほとんど(全くと言えるほど)ありません。
かつ、見る限り中が中空になっているか不明です。(後で述べますが、穴が開いている場合には分かるかも知れませんが)
従って、金属製であるので、高温に使えることは明確です。ただし、運動用には不向きであることも理解し易いと思います。
実際には高温高圧などの過酷な条件下でも高度なシール性を発揮するガスケット(シール)です。
メタルOリングの歴史とバックグランドについて
歴史的に見ますと米国の航空機用として始まったと思われます。
現在ではSAE-AS 規格になっていますが、元々MS(Military Standard)で規定されていました。
国内では規格類はありません。
その内の代表を記載しておきますと
MS 9205 Gasket-Metal O-ring, .125 Tube×.010Wall Cres
MS 9371 Gasket-Metal O-ring, .035 Tube×.006Wall, Silver Plated
MS 9373 Gasket-Metal O-ring, .062 Tube×.010Wall, Silver Plated などがあります。
お分かりのようにメタルOリングでは
めっきなしとめっき(銀)ありの種類があることになります。
ここで、TubeとはOリングで言う太さに該当して、またWallはメタルOリングのTubeの肉厚になります。またSilver Plated とは銀めっきを表現しています。
他方、材料、製造、検査などを網羅している規格(仕様書)が次のものです。
AS7325 Gasket, Metal O-Ring Corrosion and Heat Resistant Steel Procurement Specification for
この規格では使う材料を規定しています。次の2種類です。
AMS 5570 Steel Tubing, Seamless Corrosion and Heat Resistant, 18Cr- 11Ni- 0.40Ti (SAE30321)
AMS 5576 Steel Tubing, Welded Corrosion and Heat Resistant, 18Cr- 11Ni- 0.40Ti (SAE30321)
このAMS材料は、国内ではSUS321のステンレス鋼相当となります。
またこの2種類は一方がシームレス(継ぎ目なし)のチューブと他方が、溶接したチューブであることが分かり、使用の限定はしていませんので、どちらかの使用となります。
先ほど紹介しました銀めっきでは次の規格が規定されています。
AMS 2410 Plating, Silver, Nickel Strike, High Bake
銀めっき厚さは、25~38μmと規定されています。
規格AS7325についてもう少し紹介しておきます。
- 1) 用途(Application 1.2項)
主として、一般的ゴム製Oリングでは使用できない高温条件下での用途 - 2) 製造(Fabrication 3項)
- (1) 成形ではチューブを適切なローリングや成形工程でリング状にする。{解説:Oリングの太さはチューブ径で決まりますが、Oリングの径(メタルOリングはゴム製Oリングと異なり、外径が基本の径となります。)を所定径の矯正パイプのような治具にあたかもスプリングのように巻き上げて成形します。
- (2) 溶接の前段階で、成形したものを切断してその端面を清浄化しておきます。
- (3) 溶接ではフラッシュバット溶接や抵抗溶接により、切断した端面を溶接します。この溶接では、切断した端面がずれないように、かつ過度な内部溶接バリが出ないように管理するように要求されています。
- (4) 溶接部のバリの除去が、チューブ径(太さ)毎に決められた長さ範囲で求められています。
- (5) 最終成形では規定されている外径と太さになるようにすることが要求されています。
(解説:1) の成形でチューブの太さが変形―扁平になりやすいので、所要の太さになるように調整工程となります。) - (6) 清浄化(Cleaning)が要求がされています。洗浄液としては硝酸水溶液が使用されます。
- 3)特性(Properties 3.4項)
圧縮による偏り度合:溶接個所と それ以外の箇所で所定の圧縮(つぶしを与える)したときの圧縮荷重に荷重力の増加度を規定しています。
(解説:溶接時に過度の内側にバリ が発生するとその荷重力が大きくなるので、バリ状態を規制するものです。ただし、最終製品検査では実施できないので、一種のロット検査となる項目です。)
その他、品質や出荷試験項目などきめ細かく規定されています。
メタルOリングの特徴
- 1) -270℃の極低温から+700℃までの高温に使用できます。
- 2) 300MPaの超高圧から1.3×10-10Paの超真空までシールします。
- 3) シールに要するスペースが小さくてすむため、コンパクトな設計が可能です。
- 4) 他の金属ガスケットよりも、フランジの締付け力が低減できます。
- 5) フランジ用だけの用途に限定されます。
- 6) 再使用は出来ません。
メタルOリングのシール機構
メタルOリングはフランジ溝に装着し、つぶしを与えることによりその反発力で流体をシールします。チューブの種類により流体圧力7MPaを超える高圧の場合は、Oリングの流体側に穴をあけ、中空部分に流体圧を導入し、シール力を増加することにより、超高圧でもシールすることができます。
実際には穴をあけずに高圧に使用すると高圧側の側面に座屈のような現象が発生して変形するために、当然シールすることが出来ないことになります。
図1にメタルOリングのシール機構を示します。(図は三菱電線工業株式会社のものを使用しています。)
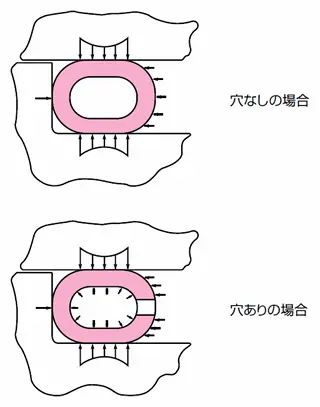
図1 メタルOリングのシール機構
メタルOリングの選定方法
メタルOリングは、温度・流体・圧力などに応じて、材料・表面被覆・形状(穴のあり・なしなど)を正しく選定しなければなりません。
- 1) 圧力については、超真空から7MPaまでは穴なしで、7MPa以上では穴をあけるタイプを選定することになります。
- 2) メタルOリングの材料は一般にはSUS321ですが、その他にはSUS316Lとインコネル600があり、選定は次のとおりとなります。
-270℃から+500℃まではSUS321とSUS316Lの材料で、SUS316Lは流体が耐食性、腐食環境など用途に用います。他方インコネル600は使用温度が-270℃から+700℃までの耐熱性が要求されるものに選定します。
他方、通常相手面の仕上げ条件にもよりますが、超真空用などでは、メタルOリングの表面に被覆が必要になります。その表面被覆材料により、耐熱性が制限されます。
表1に表面被覆と耐熱性を示します。 -
表1 表面被覆と使用温度範囲 材料 温度範囲(℃) 金 -270~+800 銀 -270~+500 ニッケル 室温から+700 インジウム -270~+130 PTFEコーティング -270~+200 例えば、インコネル材料であれば、表面被覆材料は、低温側も加味すれば、金のみとなります。
材料 | 特徴 |
---|---|
金 | 耐食性流体用、なじみが良い、耐酸性良好 |
銀 | 耐食性流体以外の標準仕様、300℃以下では金と同等のシール性能 |
ニッケル | 高温用、真空用ではフランジ面の超仕上げが必要 |
インジュウム | 低温用、軟質でめっきでは最も低締付力が可能 |
PTFEコーティング | 極低温や低温と室温とのヒートサイクル用途に最適、化学的に安定 |
なお、標準被覆厚さは40μmです。
メタルOリングの形状
図2にメタルOリングの標準の形状を示します。
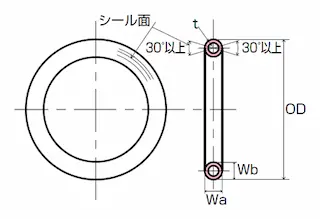
図2 メタルOリングの形状
- 1) 仕上げ方向(筋目)は図2のように円周方向に沿っていること。なお、この範囲は30°以上(両面)です。シール面の表面粗さはRa0.4が要求されています。
このことは、メタルOリングの使用がフランジ用専用であり、シール面が限定されていることからこのようになっています。 - 2) この表面仕上げは、一般に使用される場合にも、表面被覆する場合にも適用されます。
- 3) メタルOリングの場合には通常のゴム製Oリングと異なり、外径が基準となっている点に注意が必要となります。太さは通常Waが該当します。
以前に製造の規格で紹介したのですが、製造方法から均一な太さが得られないことから(円筒状の治具にチューブを巻きつけることら扁形となり易いためです)若干Wa>または=Wbとなります。
メタルOリングの使用例
図3 メタルOリングの使用例を示す。
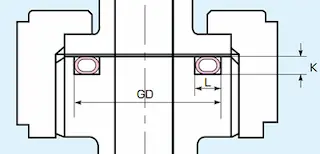
図3 メタルOリングの形状
図3はメタルOリングの使用例を示す。
この例は、一般配管の接手部で、使用しているものです。
フランジ用で、内圧の用途となります。
メタルO リングの設計
三菱電線工業株式会社のカタログを元に説明をいたします。
米国のMS図面によるものをベースにしていますので、完全なmmサイズではありません。
太さは0.89、1.57、2.39、3.18、4.77の5種類となり、チューブの肉厚と標準のつぶし量とその場合に締め付け力と弾性復元量を表3に示します。
チューブ径 [mm] |
肉厚 [mm] |
標準つぶし量 [mm] |
締付け力 [N/cm]([kgf/cm]) |
弾性復元量 [mm] |
---|---|---|---|---|
0.89 | 0.25 | 0.25 | 1716(175) | 0.04 |
1.57 | 0.25 | 0.35 | 980(100) | 0.05 |
0.35 | 2095(210) | 0.05 | ||
2.39 | 0.25 | 0.40 | 490(50) | 0.07 |
0.35 | 1225(125) | 0.06 | ||
0.50 | 1667(170) | 0.06 | ||
3.18 | 0.35 | 0.50 | 833(85) | 0.06 |
0.50 | 1225(125) | 0.05 | ||
0.70 | 2549(260) | 0.05 | ||
0.80 | 3285(335) | 0.05 | ||
4.77 | 1.10 | 0.70 | 4216(430) | 0.05 |
なお、弾性復元量とは、一旦メタルOリングを締め付けた後に、締め付けを開放(メタルOリングを溝から取り出すという状態)すると通常のゴムのOリングでは完全に元に戻るのですが、メタルOリングは完全には元に戻らず塑性変形を起こして殆ど元に戻らないことを示しています。このことは、再使用ができない要素にもなっている証拠とも言えます。
メタルOリングでは外径が基準となっています。なお、径方向での圧縮は不可能ですので、溝径とメタルOリングの外径との関係では、必ず溝径が大きく(最大でもイコール)します。真空用も内圧用と同じ設計となります。表4にこの場合の溝寸法を示します。
Oリング寸法 | GD | K | L | R | |
---|---|---|---|---|---|
チューブ径 | Oリング外径 | ||||
0.89 | ~50.0 | +0.15 Dmax 0 |
0.65±0.05 | 1.8(1.4以上) | 0.25以下 |
1.57 | ~203 | +0.15 Dmax 0 |
1.25±0.05 | 2.5(2.0以上) | 0.30以下 |
2.39 | ~100 | +0.15 Dmax 0 |
2.00±0.05 | 3.5(3.0以上) | 0.50以下 |
(100)~355 | +0.20 Dmax 0 |
2.00±0.05 | 3.5(3.0以上) | 0.50以下 | |
3.18 | ~100 | +0.15 Dmax 0 |
2.70±0.05 | 4.5(4.0以上) | 0.80以下 |
(100)~450 | +0.20 Dmax 0 |
2.70±0.05 | 4.5(4.0以上) | 0.80以下 | |
(450)~1270 | +0.30 Dmax 0 |
2.70±0.05 | 4.5(4.0以上) | 0.80以下 | |
4.77 | ~450 | +0.20 Dmax 0 |
4.10±0.08 | 7.0(6.0以上) | 1.00以下 |
(450)~1270 | +0.30 Dmax 0 |
4.10±0.08 | 7.0(6.0以上) | 1.00以下 | |
(1270)~2000 | +0.50 Dmax 0 |
4.10±0.08 | 7.0(6.0以上) | 1.00以下 |
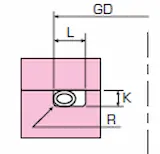
表4のGDの欄のDmaxはメタルOリングの外径を示します。
なお、外圧用は殆ど使用例がないので、ここでは省略します。しかし、設計の基本的な考え方は同じです。